Why Rubber O-Ring Core Packings Are Needed.
Rubber core packings are specialized products designed to extend the packing service life in equipment where vibration or shaft eccentricity is a chronic problem due to equipment age or excessive wear and adverse operating conditions. The internal rubber cords help the packing rings keep their intended shape under these operating conditions allowing the packing to effectively seal the equipment.
The benefits of rubber core packings have been known since at least the 1880s when patents were issued for improved steam engine packings using a combination of various fibers and natural latex.
These benefits can include: reduced leakage on agitators, hydroturbines, and equipment where shafts run eccentrically, are out-of-round, vibrate or are subject to impact.
Selection of Core Materials
Since different rubber compounds exhibit greatly differing chemical resistance, the rubber cord compound must be suitable for use in the fluid to be sealed when it is braided within the appropriate packing yarns for the application. There are several materials available depending on your exact sealing needs, the standard options are:
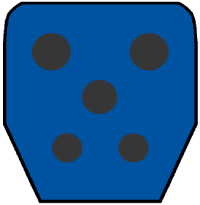
AFLAS® – NEBCO™ Vibradamp® Chemstop™ Resilient Core Packings contain chemical resistant AFLAS® rubber cords. These packing styles are intended for general services where the full range of chemical resistance of pH 1-14 is required. This quality helps provide a successful sealing solution for vibrating equipment where contamination may be an issue in corrosive products.
This packing is designated with the letters AF after the style number: NEBCO™ Style 702 AF AKⅡ®.
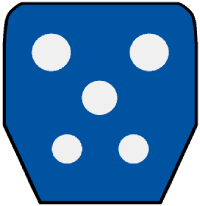
Buna – NEBCO™ Vibradamp® Resilient Core Packings contain white food grade Buna-N (Nitrile rubber aka NBR) cords for use where regulatory compliance is required. Minimum order quantities may be required.
This packing is designated with the letters PB after the style number: NEBCO™ Style 120 PB AKⅡ®.
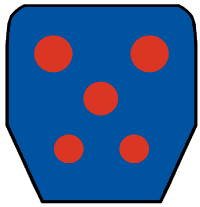
Silicone – NEBCO™ Vibradamp® Resilient Core Packings contain red silicone cords and is the most commonly used material in core packings. These packing styles are intended for milder general services.
This packing is designated with the letters SC after the style number: NEBCO™ Style 274 SC AKⅡ®.
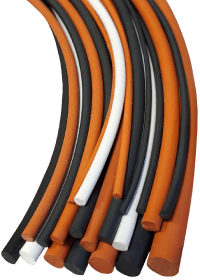
Core Packing Standards
Rubber cord stock used in compression packing can come in a variety of shapes, the standard shapes commonly available are shown below. Most manufacturers rubber core packings are produced with only a single rubber cord (solid or hollow) at the center of the braid. The problem inherent in this type of construction is the rubber cord can eventually deform within the packing due to the excessive vibration. When this occurs, increased leakage develops as the rubber cord is in a different shape/orientation than when first installed.






What Makes NEBCO™ Vibradamp® Resilient Core Packings Different?
NEBCO’s™ ANTI-KEYSTONE®Ⅱ Vibradamp® & Chemstop™ resilient core packings are manufactured with multiple, appropriately sized, evenly distributed, rubber cords in the place of axial fill yarns within the braided packing.
This creates exceptional resiliency that helps the packing maintain its intended shape and rebound faster with unstable shafts which can reduce the average fluid film thickness between the shaft and packing, while our ANTI-KEYSTONE®Ⅱ packing creates a labyrinth sealing effect to further minimize leakage. These combined benefits can be the solution where equipment instability is the problem.
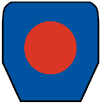
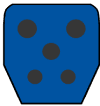

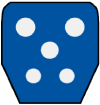
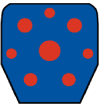
Notes on Construction: NEBCO™ Vibradamp® and Chemstop™ Resilient Core Packings contain five or more cords in sizes 3/8” (10mm) and larger. Due to size limitations, ¼” (6,4mm) and 5/16” (7,9mm) cross sections contain between one and three cords.
AFLAS® is a registered trademark of the Asahi Glass Co. Ltd
Disclaimer
*Certain styles & sizes are special order only and may be subject to minimum quantities and/or additional terms & conditions.
**For informational purposes only. New England Braiding Co., Inc. (NEBCO™) believes this information to be the best available. Any specific application you have should not be undertaken without independent study and evaluation for suitability, safety and material compatibility. No warranty is expressed or implied as each application is unique. While we have used the utmost care in the preparation of this information, we assume no liability for errors or responsibility for consequential damages resulting from the use of these products.